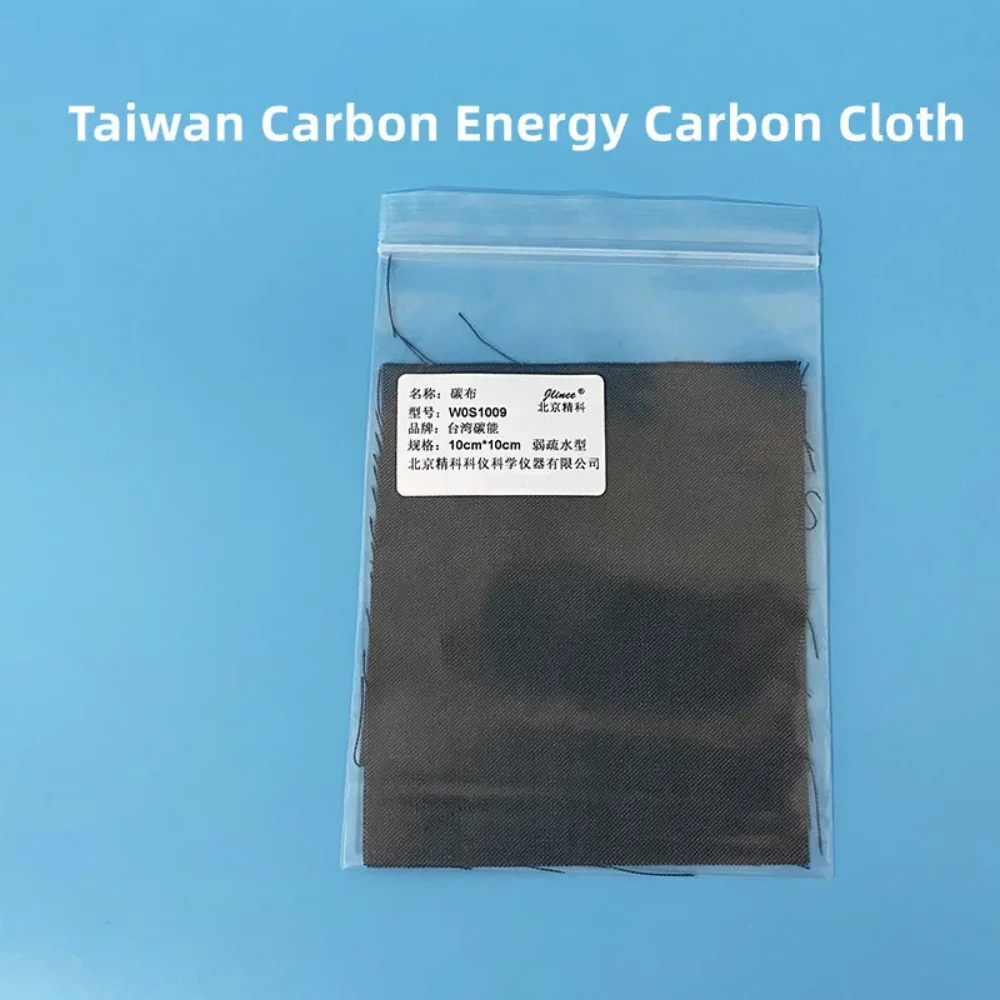
Price:
Product introduction:
Carbon cloth is generally made of PAN polyacrylonitrile as raw material, and then processed at
high temperature. W0S1011 carbon cloth produced by Taiwan Carbon Energy is a basic carbon
cloth with weak hydrophobicity, which is generally used as a substrate for material growth or
loading. If necessary, different methods such as chemical method and physical method can be
used to modify hydrophobic carbon cloth into hydrophilic carbon cloth. 10% nitric acid and 10%
sulfuric acid solution (3 nitric acids: 1 sulfur) can be used for mixing and soaking for hydrophilicity
treatment. The soaking time can be adjusted according to personal requirements for
hydrophilicity. The treatment process is at room temperature.
W0S1011 carbon cloth is a treated carbon cloth with strong hydrophobicity. Microporous layers of
MPL and PTFE are coated on the surface of the basic carbon cloth to enhance air permeability. It is
generally used as the air cathode of various fuel cells, such as hydrogen fuel cells.
Product parameters:
Substrate without MPL & PTFE Carbon Cloth
Measurement Units Method W0S1011
Thickness mm TECKOCK SM-114 0.36
Basic Weight g/m² ASTM D-646 130
Through-Plane Resistance mΩcm² Base on ASTM C-611 <5
Tensile Strength(MD) N/cm ASTMD-828 10
Tensile Strength(XD) N/cm ASTMD-828 5
Product features:
The advantage of Taiwan Carbon Energy W series conductive carbon cloth lies in its physical strength and uniform pore size, which can be enhanced by the coating of MPL. Soft, can bend 180 degrees. High strength, not easy to break. Although there are rough edges, they are not easy to spread after cutting. Good conductivity, resistivity lower than 5m Ω. cm2
Product application:
-
PEMFC(Hydrogen oxygen fuel cell: power generation with hydrogen as fuel)
-
DMFC(Methanol fuel cell: electricity generation with methanol as fuel)
-
Microbial fuel cell (using carbon cloth or carbon paper as the substrate to "grow" the biology on the substrate to generate electricity)
-
Base material of supercapacitor
Battery cathode treatment:
When carbon cloth is used as cathode of fuel cell, in addition to supporting catalyst layer C, carbon substrate layer A and gas diffusion layer B need to be supported on the other side of carbon cloth. The brief methods are as follows: A (carbon base layer), B (PTFE (Teflon diffusion layer), C (Pt/C catalyst layer)
A: Coating carbon substrate
1. Cut the carbon cloth 4 * 8 cm (two 4 * 4 cm cathodes) with a knife;
2. Weigh 50mg carbon black with an electronic balance according to the standard of 1.56 mg loaded with 1cm2 carbon cloth;
3. According to the standard that 1 mg carbon black corresponds to 12 uL 40% PTFE (Teflon, PTFE), use a pipette to take 600 uL;
4. Put carbon black into a small plastic bottle, add 6 small glass beads, add PTFE, cover the bottle, shake for 20s, and form a suspension;
5. Apply the suspension on one side of the carbon cloth with a brush, and pay attention to the slow action to avoid the carbon black from entering the other side of the carbon cloth;
6. Put the carbon cloth coated with carbon black on a cardboard, and let it stand for 2h to dry naturally, or use an electric hair dryer to accelerate;
7. Place the naturally dry carbon cloth on a high-temperature ceramic plate preheated to 370 ℃ (please wear high-temperature gloves to avoid burns) and heat it for 20-30 minutes;
8. Take the high-temperature ceramic plate out of the furnace and let the carbon cloth cool naturally, or close the furnace and open the furnace door to slow down the temperature; As PTFE has been coated on the carbon cloth, the carbon cloth will become more curly, which is normal.
B. Coating diffusion layer (PTFE, i.e. Teflon, PTFE)
(1) Fully shake 60% PTFE to ensure that the suspension is fully mixed;
(2) Evenly coat the carbon cloth with 60% PTFE solution that is shaken evenly;
(3) Remove any bubbles or large pieces of PTFE with a brush;
(4) Dry in air for 5-10 min, and the color of the coating will turn white when it is dry;
(5) Put the carbon cloth coated with PTFE into the furnace and heat it at 370 ℃ for 10-15 min;
(6) If it is naturally cooled, the color will become bright black;
(7) Repeat steps (1) – (5) for three more times, so that there are four layers of PTFE coating, which is the most appropriate diffusion layer thickness;
(8) Cut 12cm2 round cathode carbon cloth with scissors
C. Coating Pt/C catalyst
(1) Weigh 10% of the Pt/C catalyst to ensure that the 1cm2 carbon cloth has 0.5 mg of Pt, such as 6 mg of Pt for 12cm2 carbon cloth and 60 mg of Pt/C catalyst;
(2) Put the weighed Pt/C catalyst into a plastic bottle, and then use the proportion of 0.83 uL distilled water in the proportion of 1mg Pt/C catalyst, for example, 50 uL distilled water is required for 60mg Pt/C catalyst. Add distilled water drop by drop into the plastic bottle, add 6-8 glass beads, and shake for 20 s. This step is called "water treatment" of Pt catalyst;
Note: If the amount of water is not enough or is not well shaken, Pt will react with ethanol in Nafion membrane, causing heat release and even fire;
(3) According to the ratio of 6.67 uL Nafion solution and 3.33 uL isopropanol added to 1 mg Pt/C catalyst, for example, 400 uL 5% Nafion solution and 200 uL isopropanol should be added to 60 mg Pt/C catalyst;
(4) Coating the prepared paste on the other side of the diffusion layer (PTFE) of the carbon cloth;
(5) Dry the coated carbon cloth with air for at least 24h, or use low-grade heating of hair dryer to accelerate.
Reviews
There are no reviews yet.